You Ask, We Answer
We’re technical experts in the complex and ever-changing world of civil and structural engineering design and technical approval.
Will greater Electric Vehicle use affect my Multi Storey Car Park?
There have recently been concerns raised in parts of the national press about the structural implications of heavier Electric Vehicles (EVs) using existing ‘old’ Multi Storey Car Parks (MSCPs) designed for petrol or diesel cars. Those concerns cite a potential for catastrophic damage to and collapse of car park structures.
In our view, that is not the case particularly in the short to medium term. Even though the largest modern EVs are much heavier than cars produced when MSCPs were first built, a car park full of laden EVs (of about 3.5 tonnes each) will not exceed the design load commonly used for most car parks, although there will be an associated reduction of design safety factors.
The earliest MSCPs date from the early 1900’s, but many of those older structures have been demolished or are now used for a different purpose. Some hotel and apartment blocks that date from the 1930’s have underground car parks for residents, which may well still be in use. However, the majority of MSCP structures that are used today were built after the late 1940’s.
What do owners of MSCPs need to consider in relation to EVs?
- The heaviest EVs are very large vehicles and occupy a greater plan area which could not feasibly fit closely together into the ‘standard’ 2.4m x 4.8m parking spaces commonly used in most MSCPs.
- Currently EVs represent about 3% of the total number of cars in the UK, but this proportion will have to change in order to achieve the UK’s ‘Net Zero’ requirement that all vehicles must be fossil fuel free by 2050.
- Charging arrangements may well mean that EVs are clustered together as they become a more significant part of the parked vehicle proportion.
- Although the weight of EVs is unlikely to exceed design loading, the effect of significantly heavier vehicles using MSCPs will be that the condition of the structures and extent of defect, as these affect structural integrity and robustness, will become more critical to avoid structural damage.
- As a result, identifying and rectifying structural defects and having regular and robust maintenance regimes must become a bigger priority for car park owners and operators.
Link Engineering has significant experience in the investigation and appraisal of defects to multi storey car park concrete structures. This includes structural engineering appraisals of the construction condition of car parks, establishing appropriate testing regimes, evaluation of results and specifying remedial works including protection of reinforcement from corrosion.
Issues that need to be addressed in remedial and maintenance works to car park structures include: – consideration of structural condition at regular intervals; stiffness of long span decks; condition of deck coatings and waterproofing; reinforcement corrosion risk and appropriate corrosion control measures; corrosion of steel framing; condition of prestressed tendons in some precast decks; type and condition of perimeter vehicle barriers; external cladding support; treatment of movement joints.
Please contact either Nick Hirschman if you require assistance in evaluation of a car park (or any other) structure.
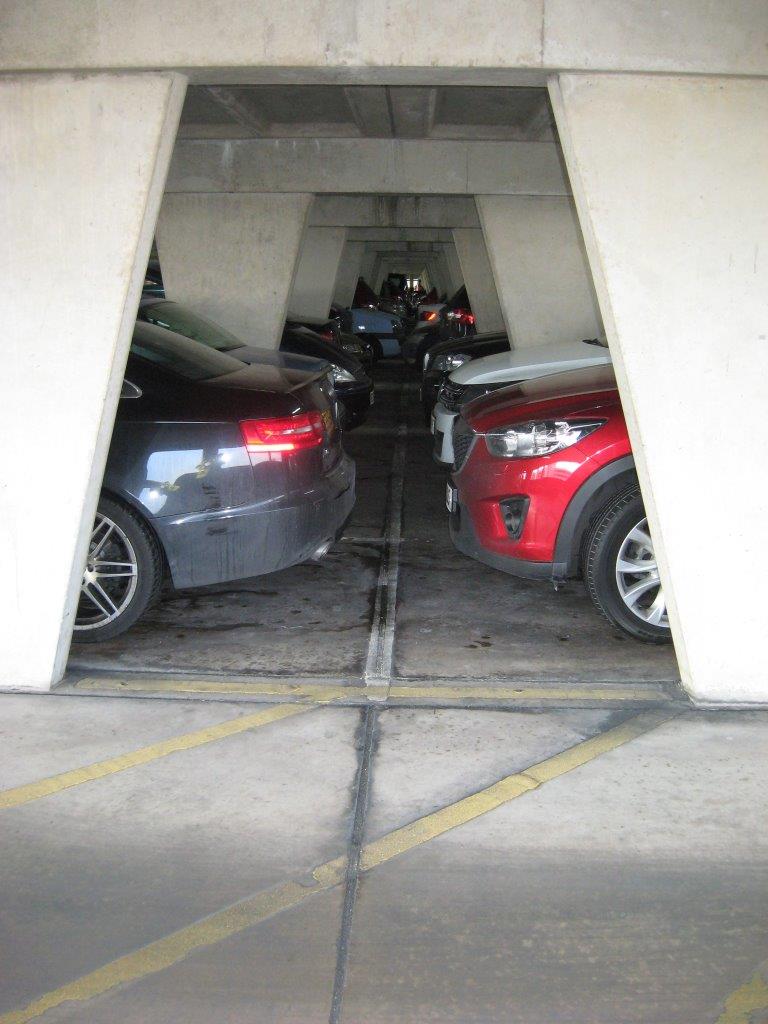
Our advice is based on the Link team’s collective experience, which includes involvement in hundreds of projects of varying scales where infiltration testing has been required to be undertaken.
On a broader spectrum, infiltration can be defined as the speed at which water passes into, or through soil. The rate at which infiltration occurs depends on the properties of the soil and the underlying geology through which the water is discharged. The capacity of the soil to infiltrate water is given by then infiltration coefficient. This is the long-term infiltration rate into the soil divided by the area of infiltration. The infiltration rate is related to a soil’s permeability, k.
It is commonly undertaken in geotechnical and hydrological assessments to review the permeability and drainage characteristics of soil.
There are several methods that are regularly used to conduct infiltration testing, two of which are falling head permeability tests and constant head permeability tests, these are usually undertaken within laboratories.
More regularly, infiltration testing is undertaken on site to potentially aid with drainage and to review the possible use of soakaways. This can be undertaken through soakaway tests.
Any soakaway test undertaken for the purposes of drainage must follow the BRE365 requirements.
The importance of using infiltration on a site is highlighted through the SuDS Hierarchy. This shows that infiltration is the ideal method of discharging surface water from a site and therefore is usually requested to be explored first.
How to undertake soakaway tests? The BRE365 test sheets state that three tests should be undertaken. The infiltration rate is measured by assessing the rate at which water infiltrates into the surrounding ground.
The below table shows typical infiltration coefficients for different types of soil, taken from the CIRIA report C753 The SuDS Manuel.
Soil type/texture | ISO 14688-1 description (after Blake, 2010) | Typical infiltration coefficients (m/s) |
Good infiltration media GravelSandLoamy sandSandy loam | Sandy Gravel Slightly silty slightly clayey SAND Silty slightly clayey SAND Silty clayey SAND | 3×10-4 – 3×10-2 1×10-5 – 5×10-5 1×10-4 – 3×10-5 1×10-7 – 1×10-5 |
Poor infiltration media Loam Silt loam Chalk (structureless)Sandy clay loam | Very silty clayey SAND Very sandy Clayey SILT N/A Very clayey silty SAND | 1×10-7 – 5×10-6 1×10-7 – 1×10-5 3×10-8 – 3×10-6 3×10-10 – 3×10-7 |
Very poor infiltration media silty clay loamclaytill | – – Can be any texture of soil described above | 1×10-8 – 1×10-6 <3×10-8 3×10-9 – 3×10-6 |
Other rock* (infiltration capacity depend on the type of rock and the extent of the nature of discontinuities and any infill) | N/A | 3×10-9 – 3×10-5 |
The infiltration coefficient values in the table are only considered to be a guide and detailed site specific investigations should be undertaken to confirm this.